Things are starting to look more floral. Yesterday, we initialized the process of prototyping the layered petals.
The very first mock-up consisted of kitchen towel, skewers and hot glue. Without too much thought, we wanted to see how the petals could be connected and unfold. In this quick and dirty mock-up, we glued together several alternating layers of two types of kitchen roll + skewers. The layers looked sort of like kites but flexible in the center. One of the layer types had skewers going out towards the corners (X) and the other type had the skewers in the shape of a window frame (+).
The result of this mock-up, as seen in the two videos below, was less than satisfactory, but not all bad. Since all the layers had the same shape, they had a tendency to lay flat on top of each other - creating less volume. Something that helped was gluing the four skewers in the top layer together, making a rigid “stem” down the center. We also found out that we liked the pointy corners in the model for aesthetic reasons. Another thing we learned from this mock up was to try making the layers in different sizes and more cone-shaped layers closer to the center.
Next up, we wanted to make a new petal mock-up that could be integrated on the previously made cardboard mock-up of the moving arms. First attempt was to see how the arms could handle one layer of petals, see video below. This time, there were 5 arms.
The result was satisfactory. The arms could move the layer elegantly. There was still a bit of jamming and the arms are still a bit out of sync, but it is only a cardboard model and we expect to iron out these issues in a higher fidelity model.
Next up, we wanted to add more layers. The kitchen roll mock-up taught us that we should try making the top layers smaller than the bottom layers. We therefore cut out 4 types of 5 identical trapezoids out of thin garbage bag. Each type had the same height and the same width at the bottom, but increasing width at the top. The 5 identical trapezoids were taped together, creating cone-like shapes in 4 different sizes. The largest was almost flat.
The inside layer (smallest cone) was taped to a rigid stem (skewer). The next layers were taped together in a net-like formation, when seen from the top. The bottom layer was taped to the existing mock-up seen in the video just above.
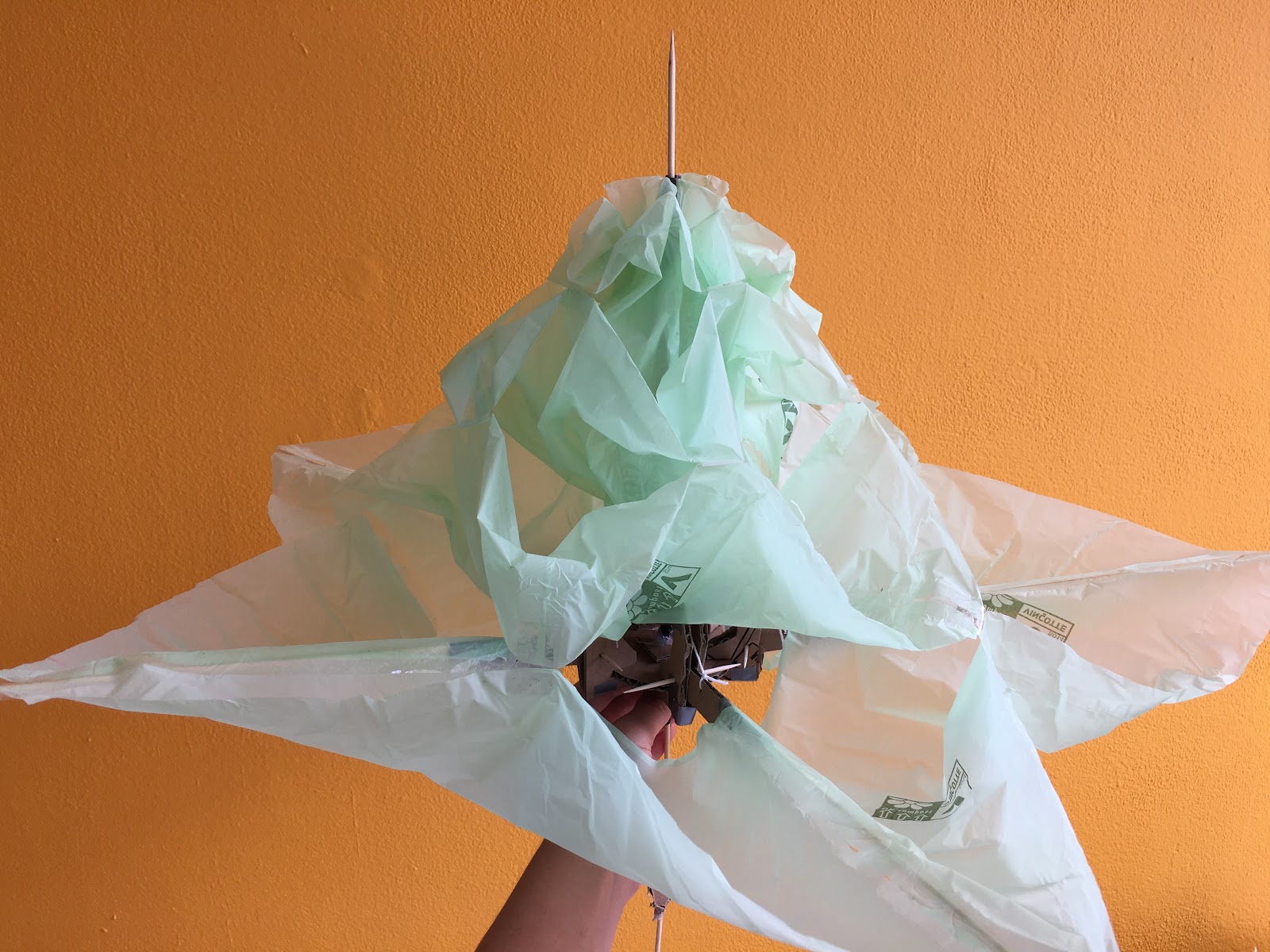
This result was far from satisfactory. It looked like a very old and tired flower. We needed some kind of stabilizers for the petals. We taped straws along the tape seams between the triangles. We thought straws would be a good choice because of their stiffness and lightness.
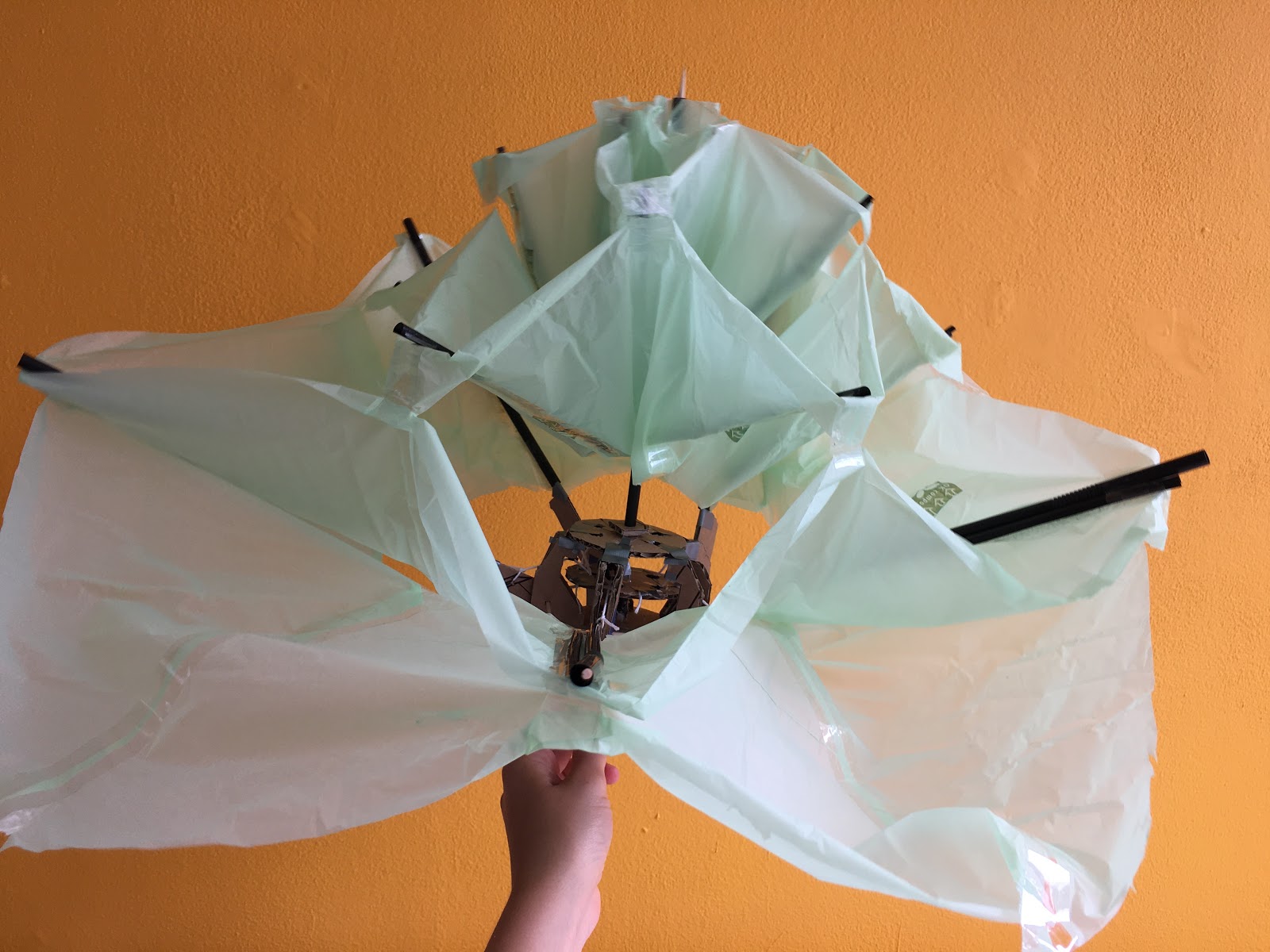
The added stiffness gave a better result. The flower got its power back.
There were however some other issues in this model:
- The petals were too heavy for the mechanical arms to lift all the way up
- We need to even out the space between the layers, adjust how much they droop, and how far out they reach
- In this model, only the outside three layers move. The inside layers are not affected by the mechanical movement. We would like all layers to move, although the outside layers will move more than the inside layers.
- The spacing between the layers is too large in the bottom. You can see the inside mechanism.
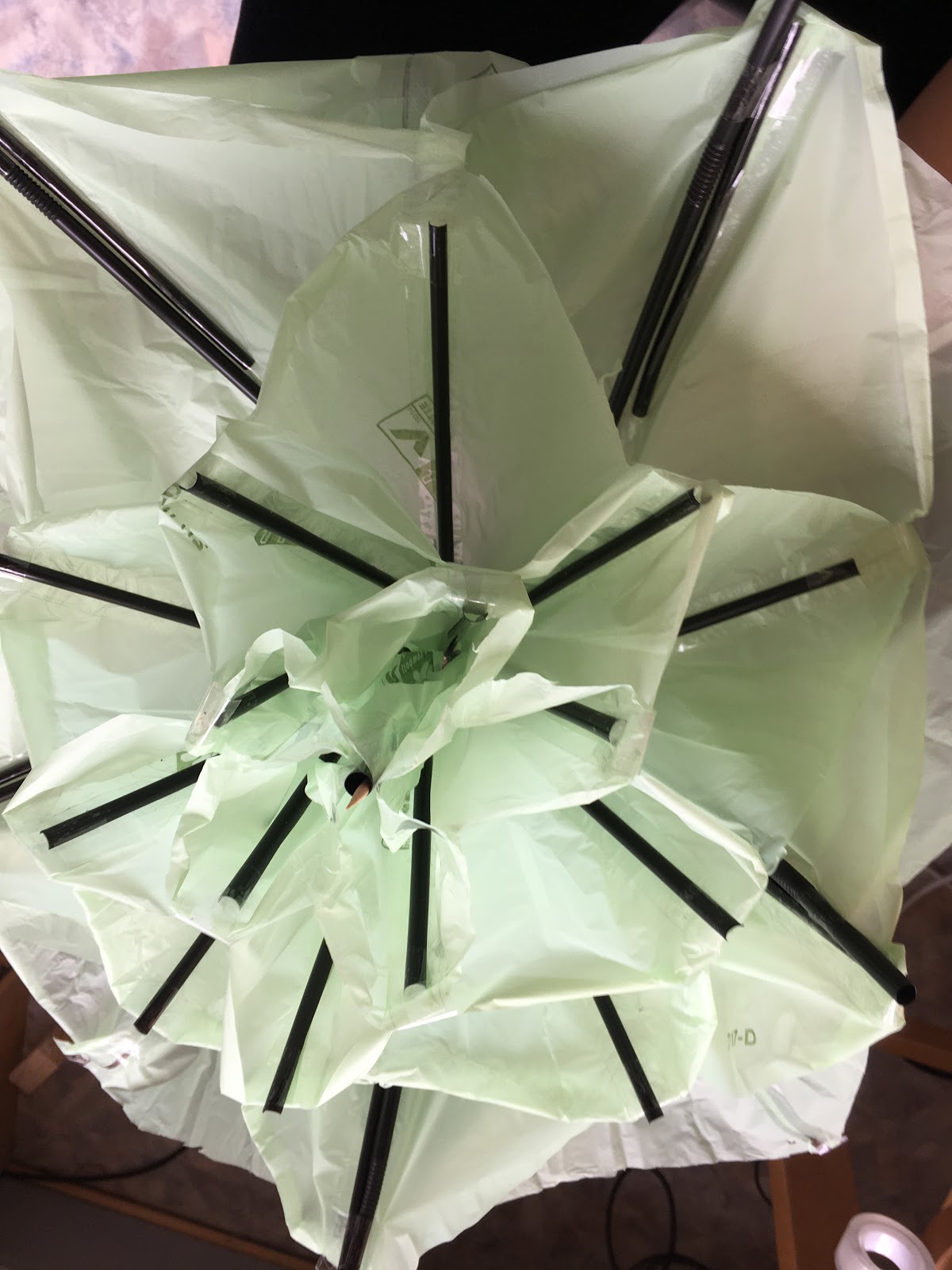
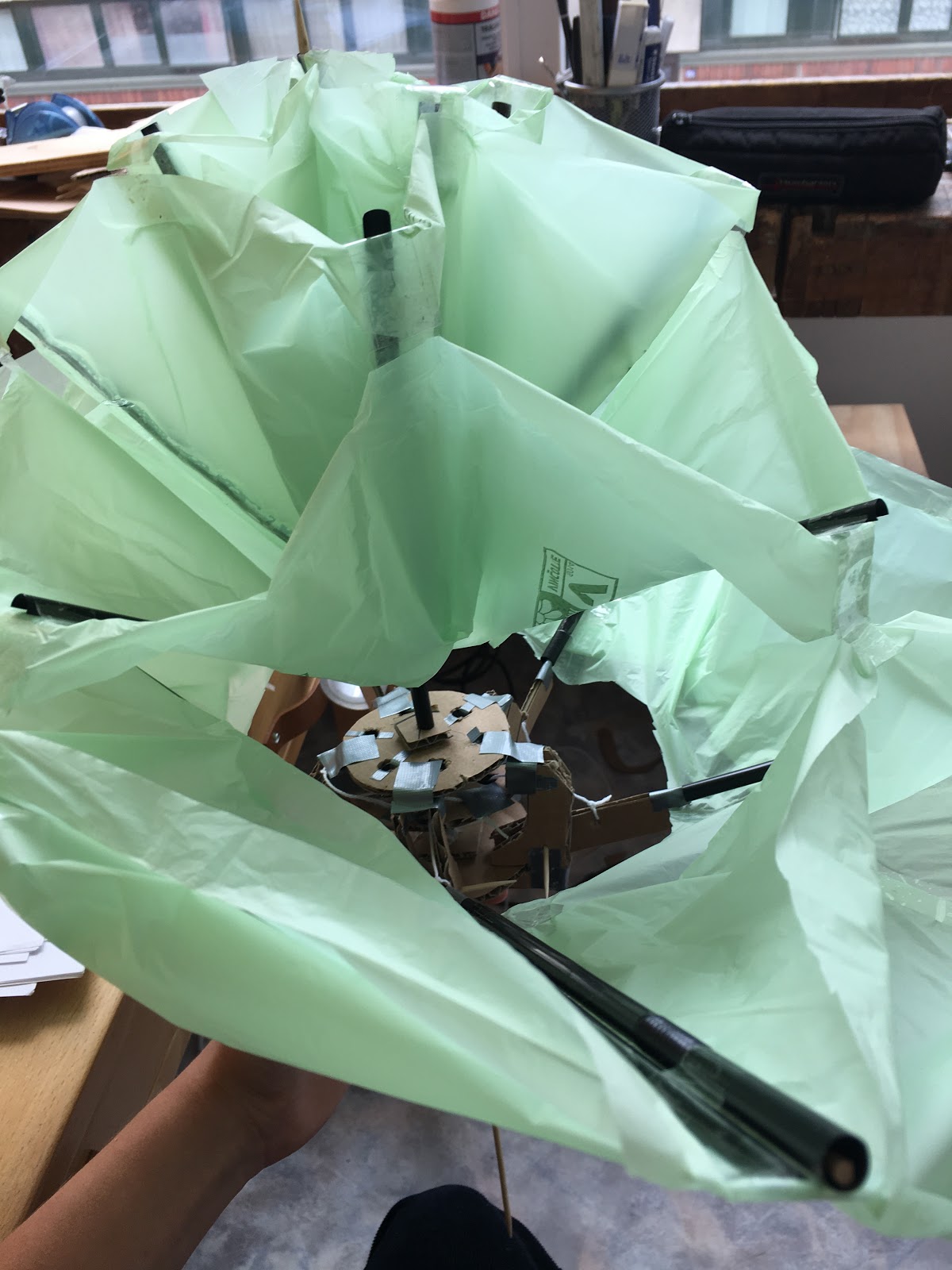
A team meeting was held at this point, where we discussed these issues and what to do about them. A major focus point of this discussion was whether or not we would like to have more layers than just the outside layer to be mechanically driven. If more layers were driven, we could possibly achieve a more elegant movement, where more layers move on their own at the same time instead of having the bottom layers pushing on the next and the next layer to create movement. The concern with having more driven layers is that the complexity level of the mechanism increases drastically. For a three week project, we think this will be too much to handle.
The discussion majorly touched on whether or not we should choose another mechanism than rotating disc with strings to lift the arms. Maybe there is another mechanism that makes it easier to have several driven layers? Maybe this mechanism will also minimize the forces required to lift the arms? After brainstorming, looking at different options with spindles, gear, several levels of string and disc etc, we decided to just keep these in mind as a back-up in case things go terribly wrong later on, but to stay with the mechanism we have. We don’t want to add more driven layers because we don’t want to add complexity at this point in the project. We would like to have a full functionality model in place before we add complexity. Also, we would like to try the string + disc mechanism in a higher fidelity, 3D-printed prototype before evaluating if the mechanism is too weak to lift the arms all the way up.
Next up, we want to make a new petal prototype. This one should be smaller, to scale, and have the same amount of layers as we want (at this point in time - 6 layers) and have even spacing between the layers.
To deal with the problem of seeing the mechanism inside, we will try to let the driving arms stand on their own and only be connected to the layered petals in their tips, see the sketch below on the left.
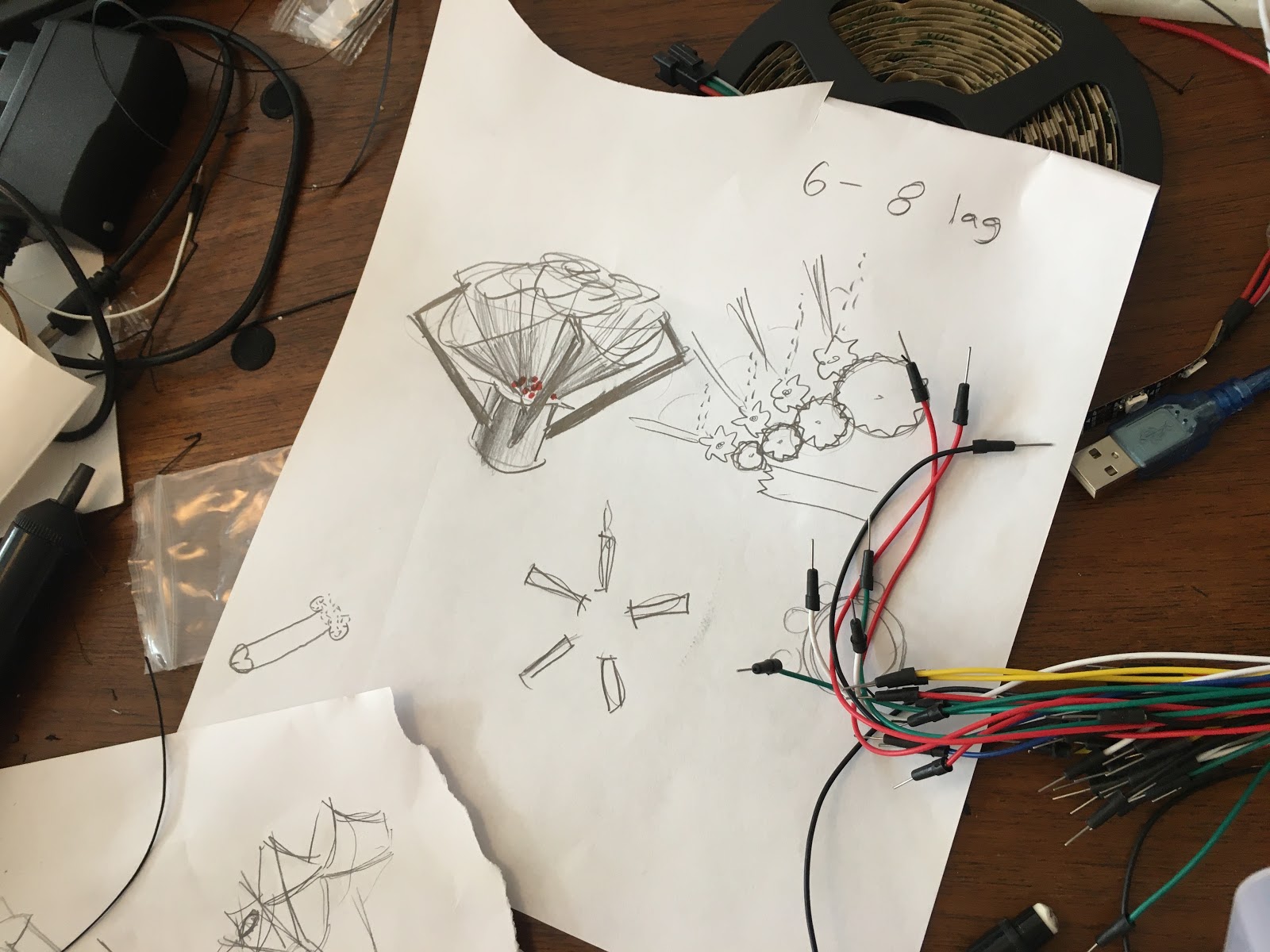
Let’s see how it'll turn out!