Since the rods had proven to be a poor mechanical choice for pulling the arms we wanted to go back to developing the idea of having strings that pull the arms up.
The problems in the last cardboard mock-up we had made was that the arms didn’t always move simultaneously and they leaned in all different directions when they were at the top. Also, the system required a lot of rotational force as soon as we added some weight to the arms - or petals. Our hypothesis was that if we made a higher fidelity model with 3D-printed parts that had less clearance, the arms would move more evenly and maybe the system could handle more weight.
The previous CAD-model for the disc + rod prototype was adjusted for string. The major difference is that the string model needs a loop to guide the string, so that the arms are pulled straight up. So, we could reuse the rotating disc and the 5 arms from the previous prototype.
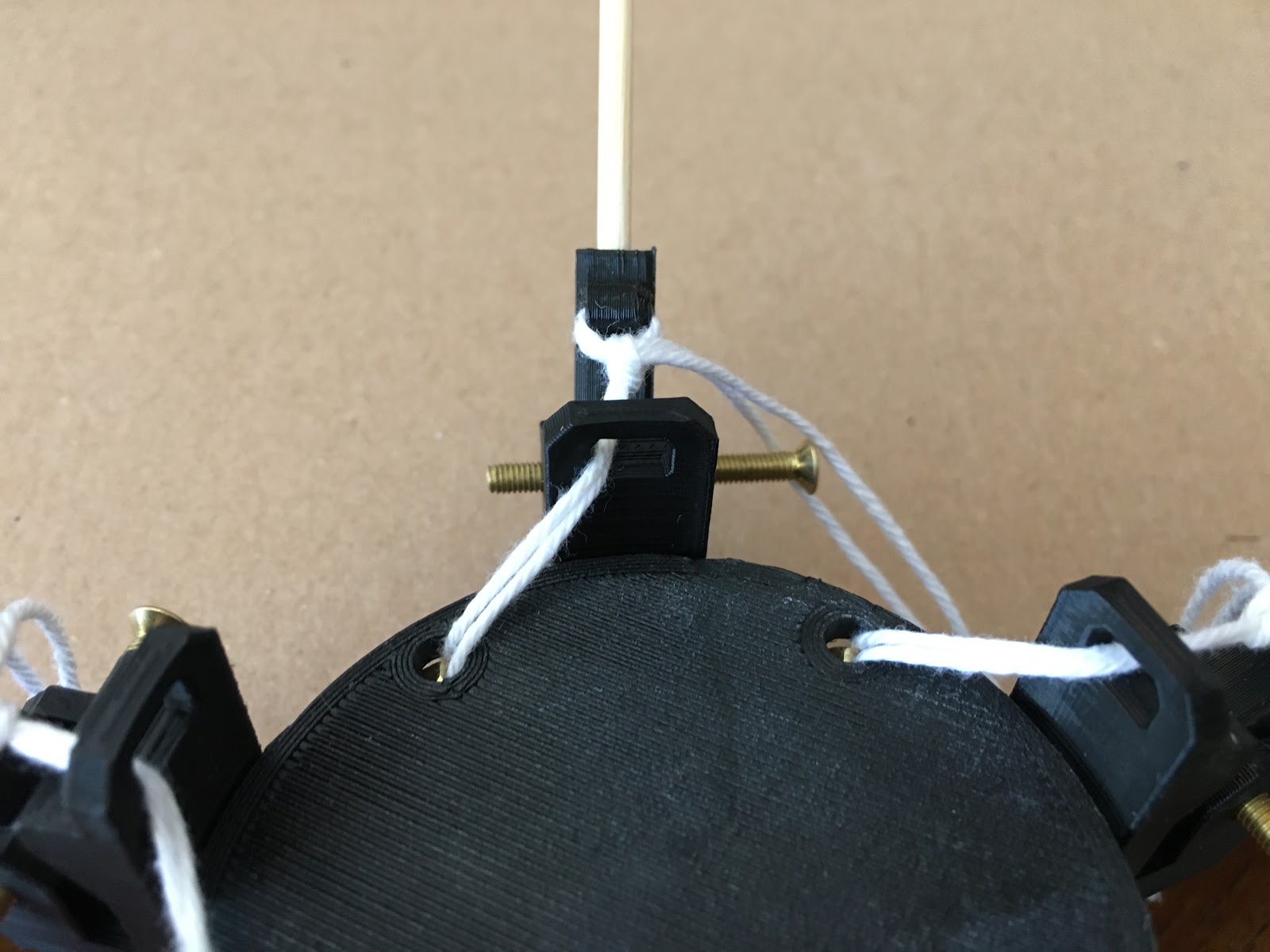
The 3D-printed parts were quickly assembled with bolts, string and skewers. The first test was to see how the system worked when activated manually (twisting the bottom using our hand).
Our theory that a 3D-printed model would make the movement more even proved itself to be correct! The little jamming we experienced, and that can also be seen in the video above, was eliminated by simply drilling some of the holes a bit larger and filing away some material here and there.
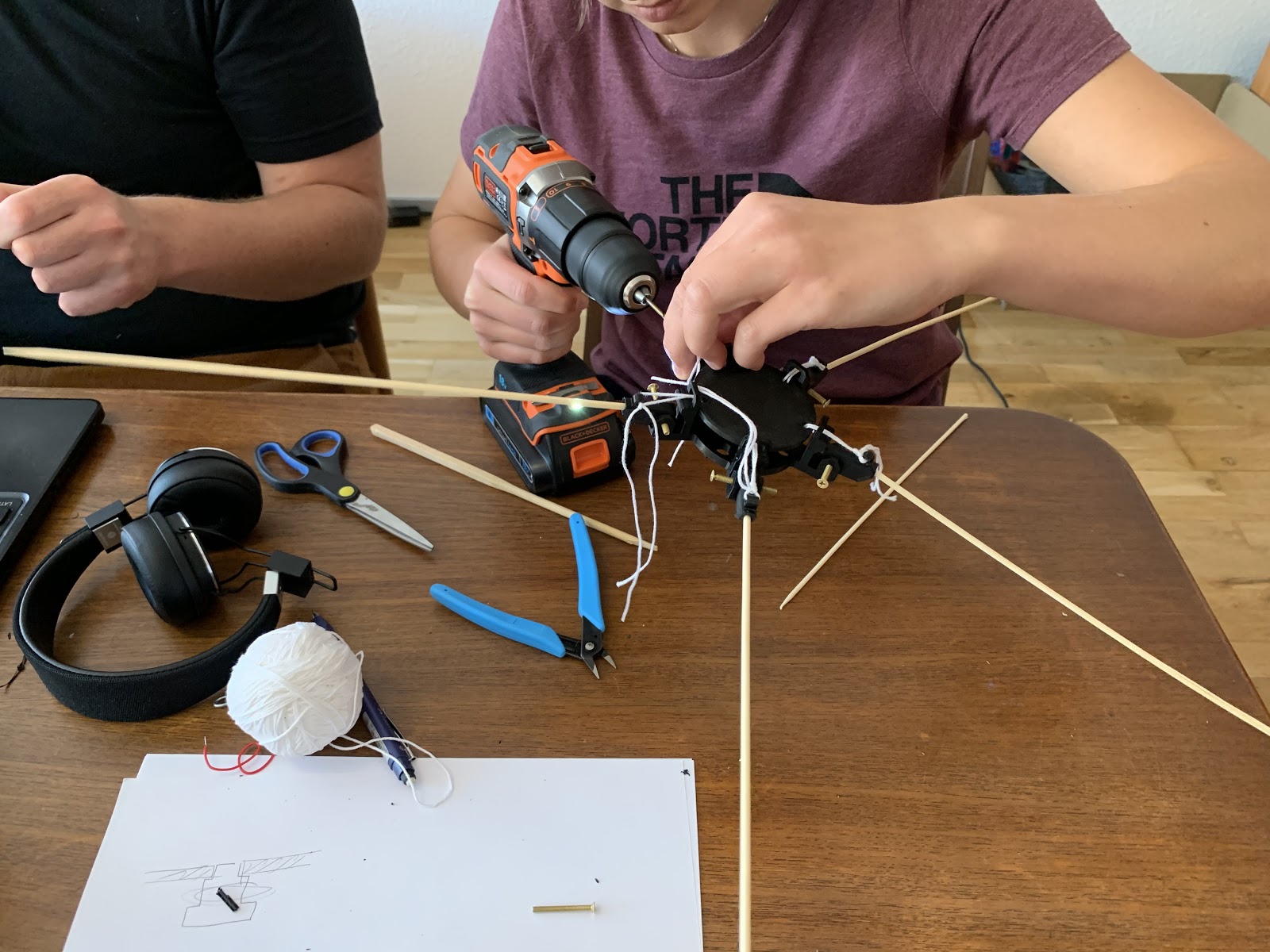
Next up, we connected the prototype to the stepper motor and ran a test script that simply had the motor turn a few degrees forth and back.
The result was very satisfying! We however found out that the motor stops when something jammed or there was too much load on the system. Since a stepper motor is not self-indexed, it will pass the original starting point on the way back, if it stopped on the way out. We need to develop a system that prevents the rotating disc to rotate too many degrees in either direction.
The next thing we wanted to test was how much weight this prototype could handle. We taped folded cardboard to the end of some of the arms. When connecting it directly to the stepper motor, the motor was too weak to handle the weight. We therefore came to the conclusion that we would like to test if gearing could be a solution to this problem.
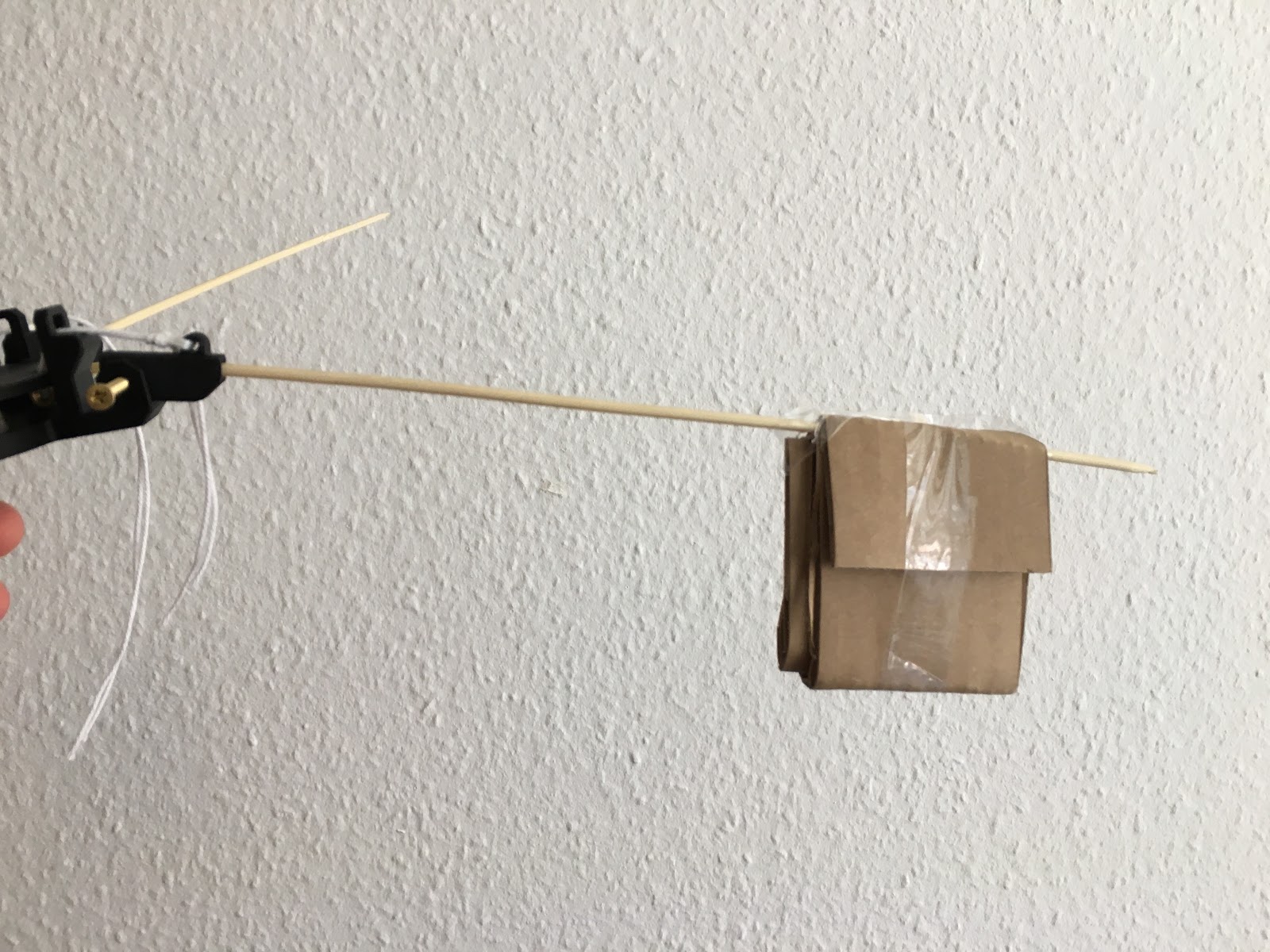
All in all - we will continue with the string-concept. Next up, implement gearing. Implement a system (perhaps buttons) that prevents the disc to rotate too far.